Different Types of Corrosion and How to Prevent It
From uniform corrosion and pitting corrosion to stress corrosion cracking and more — metal decay and attrition fall into various categories. What are these categories and how can you better prevent corrosion?
Read on as we unpack these topics.
10 Types of Corrosion
Depending on environmental factors and material characteristics, corrosion can manifest in several distinct forms — each with unique mechanisms and impacts on metal structures.
Let’s look into ten common forms of corrosion.
1. Uniform Corrosion
Uniform corrosion — or general corrosion — involves a consistent and evenly distributed attack across the entire exposed surface of a metal. It’s characterized by a uniform, predictable loss of material that leads to a general thinning of the metal over time. It can occur in metals such as steel, aluminum, and copper, often manifesting as a visible dulling, rusting, or tarnishing of the surface.
Since the corrosion progresses at approximately the same rate over the entire metal surface, the metal’s deterioration is relatively straightforward to detect and measure. The impact of uniform corrosion is significant as it reduces the structural integrity and functional lifespan of metal components by continuously weakening them until they can no longer sustain their intended load or purpose.
2. Pitting Corrosion
Pitting corrosion is a highly localized form of corrosion that leads to the formation of small holes, or pits, in the metal. Unlike uniform corrosion, which affects all exposed areas evenly, pitting corrosion concentrates its damage in tiny, discrete areas — making it much more difficult to detect and predict.
This type of corrosion is particularly insidious because a single, seemingly minor pit can compromise the integrity of an entire structure. Pits often form under a protective layer of corrosion products, hiding them from view and allowing the damage to progress unchecked.
The process initiates when the metal’s protective oxide layer is breached — due to chemical, mechanical, or environmental factors — exposing the underlying metal to aggressive agents like chloride ions. This localized breakdown leads to anodic areas where metal loss occurs rapidly, creating cavities that can become sites for further corrosive attack and even structural failure.
3. Galvanic Corrosion
Galvanic corrosion — also known as dissimilar metal corrosion — occurs when two different metals are electrically connected in a corrosive electrolyte environment. Its severity depends on the metals involved, their relative surface areas, and the conductivity of the connecting electrolyte.
This type of corrosion results from the electrochemical potential difference between the two metals, causing one metal (the anode) to corrode at an accelerated rate while the other (the cathode) corrodes more slowly or not at all.
The process begins when the more active metal (anode) starts to dissolve into the electrolyte and the less active metal (cathode) benefits from the sacrificial decay of the anode. It’s commonly observed in metal combinations like aluminum and steel in seawater, where the less noble metal (e.g., aluminum) corrodes faster than it would alone, and the more noble metal (e.g., steel) experiences reduced corrosion.
4. Crevice Corrosion
Crevice corrosion is a form of localized corrosion that occurs in confined spaces or crevices between two surfaces, such as between metal joints or where a metal meets a non-metal. This type of corrosion often arises due to differences in ion concentration and restricted oxygen supply within the crevice, compared to the open environment.
Factors like pH, chloride concentration, and environmental temperature, along with metal composition and geometrical features of the crevice, play central roles in accelerating this corrosion process.
5. Stress Corrosion Cracking
Stress Corrosion Cracking (SCC) is where materials crack due to the simultaneous presence of tensile stress and a corrosive environment. This type of corrosion can occur under mechanical stress: either from external sources like load-bearing or internal factors such as residual stresses from manufacturing processes.
SCC often results in microscopic cracks that develop in a direction perpendicular to the stress. These cracks may be either intergranular, following grain boundaries, or transgranular, cutting across grains. It’s insidious as it commonly causes significant structural failures with little to no prior indication, with the material typically showing minimal external damage before failure.
6. Intergranular Corrosion
Intergranular corrosion is a localized form of corrosion that affects the grain boundaries of a metal — leaving the bulk of the metal relatively intact.
It takes place when there are chemical or structural differences at the grain boundaries compared to the interior of the grains. More specifically, it can occur due to impurities, segregation of alloying elements, or depletion of structurally crucial elements like chromium in stainless steels, for instance. Such variations create weaker zones that are more susceptible to corrosion than the rest of the metal.
7. Erosion Corrosion
Erosion corrosion is the accelerated degradation of metal due to the combined effects of mechanical erosion and chemical corrosion, typically triggered by the rapid movement of corrosive fluids against the metal surface.
This process is characterized by distinctive grooves and surface irregularities that reflect the directional flow of the medium. It’s particularly prevalent in softer alloys such as those of copper, aluminum, and lead — where even protective surface films can be compromised under high fluid velocities.
Factors such as turbulence, cavitation, and impingement intensify the damage. This often manifests as pitting in specific locations, including the inner surfaces of pipes, areas of turbulent flow caused by constrictions, and sharp bends in the piping system, among others.
8. High-Temperature Corrosion
High-temperature corrosion is a chemical degradation process that impacts materials exposed to environments above 400°C (750°F). Naturally, this corrosion type is prevalent in industries such as power generation, aerospace, and chemical processing, where each metal component is subjected to aggressive gasses, molten salts, or metals.
The main forms of high-temperature corrosion include:
- Oxidation.
- Sulfidation.
- Carburization.
- Nitridation.
9. Concentration Cells Corrosion
Concentration cell corrosion is a form of galvanic corrosion that occurs when parts of a metal surface are exposed to different concentrations of the same electrolyte, leading to varying electric potentials across the surface. This difference in electric potential causes certain areas of the metal — known as anodic areas — to corrode more rapidly than others. These anodic areas are typically those in contact with lower concentrations of the electrolyte, where the metal tends to dissolve into ions to balance the concentration across the cell.
The mechanisms behind concentration cell corrosion include:
- Differential aeration, where varying oxygen concentrations create anodic and cathodic areas.
- Ion concentration cells, where variations in salt concentrations lead to similar effects.
The most common sites of this type of corrosion are under deposits, in crevices, or any areas that experience restricted oxygen supply. This localized corrosion often leads to substantial material degradation, typically appearing as pitting or crevice corrosion, thereby compromising the structural integrity of the metal.
10. Salt corrosion
Salt corrosion, also commonly called saltwater corrosion, occurs when metal surfaces come into contact with salt and water, leading to accelerated chemical reactions that cause the metal to oxidize and degrade. Naturally, this type of atmospheric corrosion is particularly common on vehicles and structures exposed to road salts or marine environments.
Salt corrosion can cause significant material damage, resulting in pitting, loss of metal, and ultimately structural failure of affected components.
Corrosion Resistance and Prevention: Best Practices
The preventative and mitigative measures you take will largely depend on your product’s specific environmental exposure, material composition, and operational requirements.
In general, consider adopting:
- Cathodic protection: This method involves using a sacrificial anode made of a more reactive metal. When attached to the metal that needs protection, the anode corrodes instead of the protected metal, effectively diverting the corrosive process away from important structures.
- Hot-dip galvanization: In this process, metal components are coated with a layer of zinc by immersing them in a molten zinc bath. The zinc layer serves as a protective barrier that prevents corrosive substances from reaching the underlying metal and also acts as a sacrificial anode when exposed to corrosive environments.
- Barrier coatings: These involve applying a non-conductive film — such as paint, epoxy, or plastic — over the metal surface. A protective coating acts as a physical barrier, blocking corrosive agents from coming into contact with the metal, thereby significantly slowing down the corrosion process.
Also, ensure that your products are adequately tested. Testing chambers act as accelerated environments that simulate various corrosive conditions, allowing you to evaluate their resistance to corrosion and identify potential weaknesses.
Prevent Corrosion with Auto Technology
At Auto Tech, we’re the premier manufacturer of high-quality innovative environmental corrosion testing equipment. For over 75 years, our expertise, products, and services have consistently met and exceeded even the most demanding needs of our customers’ products.
Our corrosion testing products span a broad range of applications from automotive and aerospace to industrial and military, offering solutions that comply with international standards.
Learn more about Auto Technology’s full range of corrosion testing solutions.
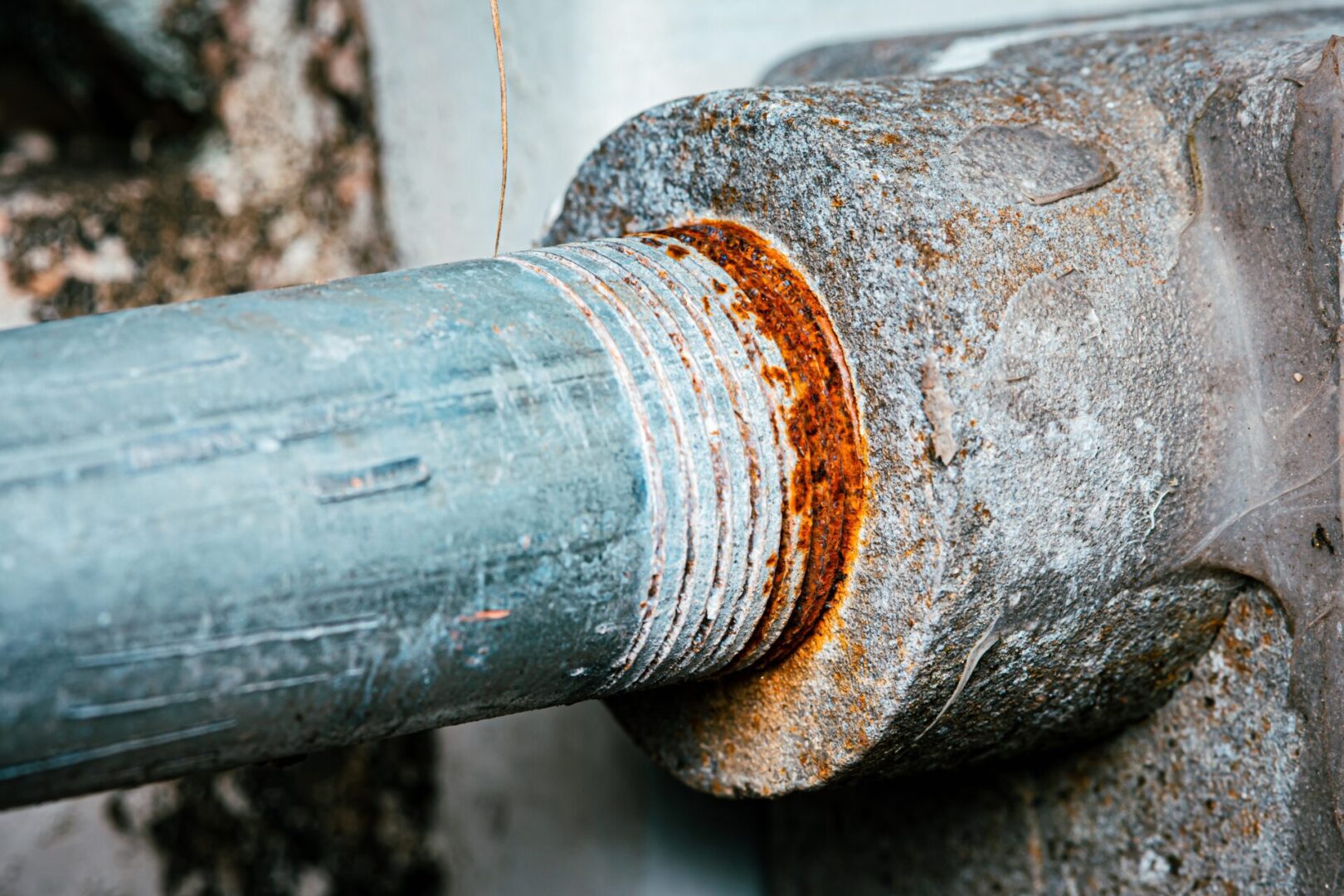