What Is Cyclic Corrosion Testing?
Manufacturers rely on cyclic corrosion testing to ensure products can withstand varying environmental conditions and maintain their integrity over time. That way, they can improve product durability, reduce the risk of failure in actual usage conditions, and better adhere to regulatory requirements.
Read on to learn more about cyclic corrosion testing, how it compares with salt spray testing, and the available market-leading testing solutions.
The Purpose of Cyclic Corrosion Testing
Cyclic corrosion testing works to simulate real-world corrosive conditions in a controlled environment, allowing analysts to predict the longevity and durability of materials under varying climatic influences. This form of environmental testing alternates real-world conditions within a test chamber, exposing the material to cycles of salt fog, humidity, and drying periods to replicate the natural wear and tear that occurs over time.
The process involves placing samples in a cyclic corrosion test chamber that can control and alter conditions: temperature, humidity, the presence of corrosive agents, and others. This chamber is designed to automate environmental changes, ensuring consistent and repeatable results. The outcomes from these tests enable engineers to assess potential weaknesses in material designs and develop strategies to improve product resilience against corrosion.
The main function of cyclic corrosion testing is to evaluate the performance of materials and coatings in environments that mimic the fluctuating conditions they’ll encounter in actual use. For example, automotive parts — which are often exposed to road salts, moisture, and temperature variations — are tested to determine their reaction to these elements over extended periods. This testing provides data on how different materials degrade or resist corrosion when subjected to cycles of exposure, similar to those experienced in everyday vehicle operation. This information helps in refining product specifications and improving the overall design of automotive components to ensure they meet the required standards of performance and reliability.
Cyclic Corrosion Testing vs. Salt Spray Testing: Which Should You Choose?
The traditional salt spray test, which has been employed for decades, assesses the corrosion rate of metals. In this test, salt — an accelerator of corrosion — is dissolved to create a solution that forms a “salt fog.” This fog is then sprayed onto the material within a controlled environment inside a salt spray test chamber
Using failure analysis, the analyst determines the corrosion rate in the salt fog. They analyze the data to devise a tailored corrosion-resistant solution suited specifically for the metal in question. Typically, this solution involves applying a protective coating to the exposed metal.
Through salt spray chamber testing, manufacturers and researchers can accurately measure the durability of protective coatings under accelerated corrosive conditions, enabling them to optimize materials for longer-lasting performance. Moreover, it provides a cost-effective means to simulate years of environmental exposure, allowing for the assessment of material degradation over time without the need for long-term outdoor environmental testing.
The choice of corrosion testing method largely depends on the intended use of the metal. For instance, steady-state salt fog testing might be preferable if the metal is expected to remain in a consistent environment, such as being submerged in saltwater. Other contexts where salt spray testing may be preferable over cyclic corrosion testing include:
- Outdoor fixtures and fittings in maritime locations: For materials that are permanently installed in places like docks, piers, or seafronts, where constant exposure to salt air is the main corrosive factor.
- Automotive parts used in coastal regions: Vehicles in coastal areas face continuous exposure to salty air, making salt spray testing ideal for evaluating the effectiveness of rust prevention treatments on car components.
- Construction materials for marine infrastructure: Building materials used in marine settings such as bridges, ship hulls, and offshore platforms benefit from salt spray testing to assess their long-term resistance to a static salty environment.
- Aerospace components: For parts that are exposed to similar conditions throughout their service life, such as certain aircraft components that operate in marine climates or near oceanic environments.
On the other hand, cyclic corrosion testing is better suited for materials that are exposed to varying environmental conditions. This includes automobile bodies, for example, as they experience conditions similar to those simulated in the test: changes in temperature, humidity, and more. This testing provides a more accurate depiction of the metal’s corrosion rate, leading to more effective protective solutions.
Ultimately, manufacturers and product developers should choose the testing method that best matches the real-world conditions their products will face. At Auto Technology, we offer both cyclic corrosion testing and salt spray testing solutions that cater to your specific product requirements. If you’re unsure which solution is best suited to you or of the capabilities of the solutions themselves, please reach out to one of our team members.
No Matter the Method, Auto Tech Offers a Superior Solution
At Auto Tech, we offer next-generation corrosion chamber testing solutions that allow companies to ensure the durability and reliability of their products
Auto Technology’s Salt Spray Testing Solutions
Our salt spray testing equipment is designed to accommodate both standard and specialized corrosion chamber testing protocols, ensuring versatility across diverse industrial applications.
Walk in salt fog corrosion test equipment: This equipment is specifically engineered to handle larger test specimens. The chamber’s interior includes a sloped ceiling according to ASTM B117 specifications to prevent condensation from affecting test samples. With a comprehensive PC-based control system, the equipment ensures precise environmental conditions and features such as horizontal dispersion tubes with atomizer nozzles for uniform salt fog distribution. These chambers are ideal for rigorous testing requirements, providing reliable and replicable conditions to assess the corrosion resistance of large-scale materials and assemblies.
Multipurpose salt fog test equipment: MPF equipment supports a wide spectrum of corrosion tests, including salt fog, humidity, and cyclic testing under ASTM G85 Annex A5, among others. The unit is equipped with a microprocessor-based control system for accurate environmental adjustments and an ATO-Fill System for automated solution management. This chamber is suitable for the automotive industry and other industrial applications requiring detailed and repeated exposure to corrosive environments.
Salt fog cabinet: The Standard Salt Fog Cabinet functions to meet rigorous and traditional corrosion test specifications such as ASTM B117 and Mil-Std 810D. The cabinet features a smoke-gray transparent PVC lid for easy sample monitoring and inert white PVC lining for added durability against corrosive environments. Equipped with digital temperature controllers, a Unifog Dispersion Tower for uniform salt spray distribution, and an ATO-Fill System for continuous operation, this cabinet is suitable for standard salt fog and humidity tests in a variety of industrial applications.
Click here to learn about our full range of salt spray testing solutions.
Auto Technology’s Cyclic Corrosion Testing Solutions
Auto Technology’s Cyclic Corrosion Testing (CCT) chambers deliver reliable testing outcomes by simulating a variety of environmental conditions that replicate real-world corrosive atmospheres. These chambers provide the capability to automate sequences of testing cycles, such as salt fog, humidity fogging, dry, dwell, and controlled humidity cycles. The CCT chambers can also accommodate solution spray and wet bottom relative humidity as optional settings. Each of these cycles can be programmed to operate in any sequence and for varied durations, enabling precise adherence to industry standards and specific testing protocols.
Moreover, the CCT chambers resist the corrosive effects of the solutions used within, ensuring longevity and consistent performance. Its construction also naturally insulates the chamber, helping to maintain stable conditions that yield accurate and repeatable results. The chambers are capable of temperature variations from -20°C to 90°C, with humidity levels adjustable from ambient up to 100% during high humidity phases, and below 30% during dry-off cycles.
Control options include a standard programmable logic controller (PLC) with an easy-to-use text interface, or a more advanced computer-based control system that offers extensive data logging capabilities and graphical monitoring of test conditions. These control systems are designed to store multiple test profiles, which can be customized and easily updated to meet evolving testing requirements.
If you’re interested in learning about how our cyclic corrosion testing solutions can benefit your specific applications, please reach out to our team for more detailed information and a personalized consultation.
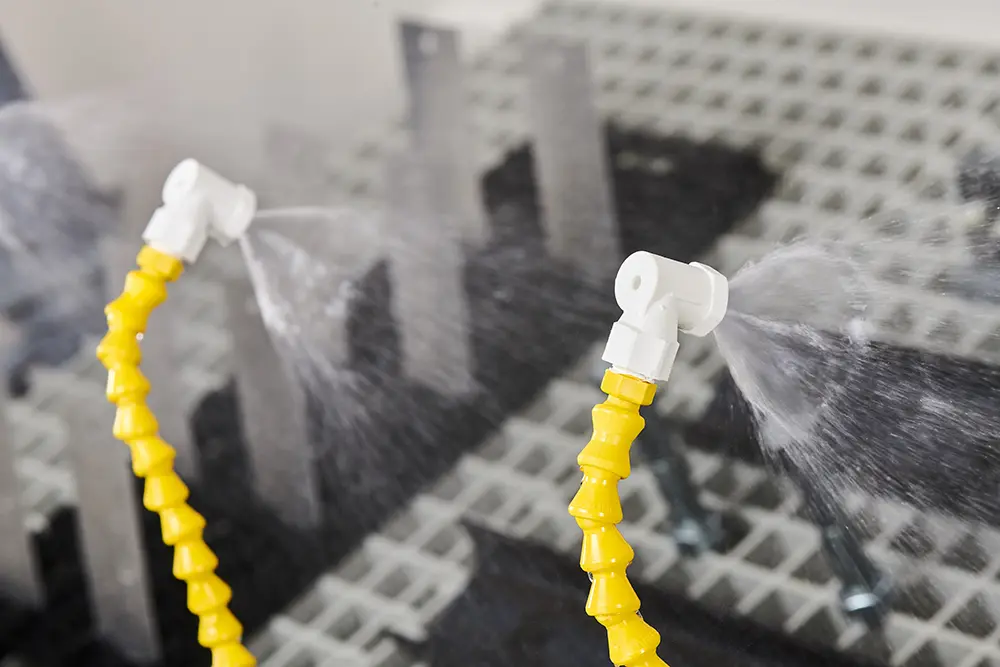